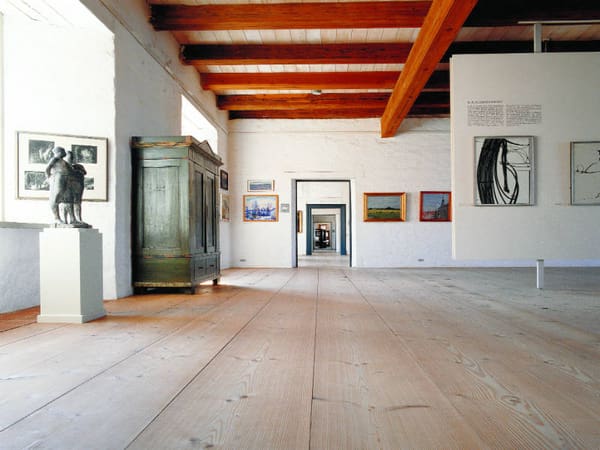
Historien om Dinesen – et dansk kvalitetsprodukt i træ.
Jels Savværk i Sønderjylland er blevet til den internationale virksomhed ’Dinesen’ – en sjælden succeshistorie i dansk træindustri. Produktet er trægulve af douglas eller eg, efterspurgt af førende arkitekter i bl.a. England, USA og Japan. Og af en del danskere med sans for kvalitet. Flot produceret og dygtigt markedsført. Som de selv udtrykker det: Dinesen er ikke et produkt – det er en passion.
I Sønderjylland ligger et savværk. Eller rettere lå et savværk: Jels Savværk. Det var et af de 6-800 savværker, som kunne findes spredt ud over landet i 1950’erne. Nu er der ifølge Dansk Industri kun 22 tilbage.
De mange savværker forsvandt i den benhårde konkurrence, hvor stort er godt, og småt er svært. Det største danske savværk skærer i dag omkring 250.000 m2 træ om året. Det nord(øst)tyske savværk, som blev bygget med statstilskud efter murens fald, og som har taget meget træ fra Danmark, skærer op mod en million kubikmeter. Det samme gør en række svenske savværker. Men selv om stort skal være godt, så kører mange af de store savværker i Tyskland, Sverige og Danmark alligevel med røde tal på bundlinjen.
Hvad gør man, hvis man vil overleve som en dansk træindustri i den situation? Man finder sig en niche!
Det er, hvad Jels Savværk har gjort. Det blev grundlagt i1898 af bygmester Hans Peter Dinesen. Savværket kørte i mange år helt traditionelt med et bredt sortiment på hylderne. Det blev sagt, at hvad man ikke kunne få på apoteket, det kunne man få nede på savværket. Sådan er det gået i arv gennem fire generationer Dinesen.
Fra traditionelt savværk til træindustriel nichevirksomhed
Da Skovdyrkeren kommer på besøg en efterårsdag i september får vi bl.a. historien om, hvordan det traditionellesavværk fandt frem til sin helt egen succesfyldte niche.
I 1965 fik man en henvendelse fra de to arkitekter, der var i gang med en restaurering af det 400 år gamle Sønderborg Slot. Arkitekterne spurgte, om savværket kunne levere specielt lange og brede planker til de store sale. Pommersk fyr, som man anvendte før, kunne ikke opdrives. Men der kunne leveres i douglas, og således endte det med, at Jels Savværk blev leverandør af 15 meterlange og op til 45 cm brede gulvplanker af douglas (se billedet øverst, samt billedet på dette blads forside).
Det blev starten på den produktion, der efter nogle år skulle ende med at blive forretningens hovedprodukt. Efterspørgslen var der, først fra andre slotte, herregårde og kirker, derefter også fra private bygherrer.
Som et særligt produkt har man desuden leveret det man kalder ’historiske planker’. Det er planker, som er savet, så de følger stammens form, det vil sige, at de er bredere ved roden end i toppen. Fidusen er her, at man på den måde opnår den optimale udnyttelse af stammerne. Efter denne opskæring lægger man plankerne rod mod top, hvilket igen kræver, at de forsynes med not i begge sider, og at der arbejdes med løs fer.
Traditionelt har man udelukkende arbejdet i douglas. Men langsomt er man kommet ind på eg som et alternativ, og nu udgør andelen af egegulve mere end 30%.
Hvor kommer træet fra?
Hvad angår douglasen må savværksejer Thomas Dinesen tilstå, at stort set alt råtræet kommer fra Tyskland.
Til en start fik man leverancer fra Silkeborg-området, men dels er ressourcen i Tyskland meget større, dels var det erfaringen, at det var lettere at få en god og fleksibel betjening i Tyskland.
Meget træ kommer fra Schwartzwald omkring Freiburg. Her er meget dygtige producenter, der holder en linje i produktionen årti efter årti (en af de ejendomme, hvor man køber, har været i familiens eje i 500 år). Det må være det, man kalder kontinuitetsskov. Træhøjden er 50-65 meter. Topdiameteren på de kævler, man køber, skal være minimum 40 cm. Kvaliteten er meget vigtig – man kan kun bruge 3-5% af de stammer, der er store nok, og her køber man kun den nedre del af stammen.
En del af det træ, man køber, er opstammet. Det er dog ikke afgørende for savværket, men Thomas Dinesen vurderer, at det faktisk kan betale sig for skovejeren. Men her er det afgørende, at det gøres rigtigt.
Jels Savværk er den største opkøber af douglas i Europa. Der købes for tiden 10-15.000 m2 rundtræ om året. Anderledes forholder det sig med egen. Her indkøbes kun færdigskårede planker. Det meste købes på Herskind Savværk, og en del af egetræet er faktisk dansk.
Man vil ikke ind i andre træsorter. Slet ikke tropisk træ, selv om der her findes træsorter med fortrinlige tekniske egenskaber, og selv om man kunne få dem med certifikat og det hele. Historien vil være for svær at fortælle, kontakten med skoven for vanskelig, troværdigheden problematisk – og man har ikke behov for det.
Certificering
Savværket er certificeret, først FSC® og snart også PEFC. Men det vigtige for savværket er ikke det stykke papir, der følger med et certifikat. Der findes certificeret træ, som ikke er bæredygtigt produceret. Og der findes træ uden certifikat, som lever op til de højeste standarder. Det vigtigste for Thomas Dinesen er derimod de holdninger og værdier, som findes hos de skovejere, man arbejder sammen med. Og dem kan man stå inde for.
Man har den særlige politik, at hvis en kunde insisterer på at få certificeret træ, så kræver man, at han tager træ i faldende længder og i blandede bredder. Ud fra det ræsonnement, at når han vil have certificeret træ, så må bæredygtighed ligge ham så meget på sinde, at han også ønsker at få den opskæringsform, der giver mindst spild!
Forarbejdning
Rundtræet af douglas skæres op til planker (lønskæres) hos et antal lokale, tyske savværker, så det kun er plankerne, der transporteres til Jels til videreforarbejdning. Denne består i tørring, kapning på længde og bredde, kvalitetssortering, høvling, fræsning af not og fer samt reparation af fejl, først og fremmest i forbindelse med knaster. Endelig naturligvis sortering og pakning til kunderne.
Under processen bores de døde knaster ud og der bankes propper i, lavet af rundstokke af douglas. Råvaren er kostbar, og der skal tages vare på den så godt det er muligt.
Det samme gælder egen. Egeplankerne har det med at flække i enderne under tørringen. For ikke at værenødt til at skære dette fra, indsætter man ’svalehaler’ tæt ved enderne på en del af plankerne. Herved kan de anvendes i fuld længde. På den måde vender man et problem til en fordel, idet plankerne ved denne behandling får et gedigent indtryk af håndlavet kvalitet (hvad det jo faktisk også er). Denne sortering kaldes Dinesen Heart Oak.
Salg
Alt salg er direkte til kunden uden mellemled. Det har først og fremmest den fordel, at man har føling med træet helt ud til den bygning, hvor det skal ligge. Herved minimerer man de problemer, der kan opstå, hvis gulvplankerne ikke opbevares eller lægges korrekt, og som altid vil falde tilbage på savværket.
Det direkte salg er en mærkesag for virksomheden, men kompliceret, idet der eksporteres til 30 lande. Ud af de 80, ansatte arbejder de 45 i administrationen, hvoraf de 17 er sælgere. Hver kunde oprettes som et projekt, der tilknyttes sin egen sælger, som så rådgiver vedrørende valg af produkt, om betydningen af fugtforholdene i huset, om lægning af gulvet og om efterbehandling.
Mange gulve produceres specifikt til den enkelte kunde. Det forekommer ofte, at sælgeren besøger byggestedet, og det har i enkelte tilfælde været aktuelt at tage kunden med ud i skoven, før træet fældes.
Man arbejder på omkring 2000 projekter ad gangen, idet mange projekter strækker sig over ganske lang tid. I alt har man leveret flere millioner kvadratmeter gulv, siden man startede.
Man har et godt samarbejde med en række arkitekter i ind- og udland. I London har man blandt andet etableret sig i Saatchi Gallery, hvor Dinesen er ’Founding Patron’ og har sponsoreret godt 5.000 m2 gulv. Galleriet fungerer også som showroom. Andre showrooms findes bl.a. i København og i Oslo. Til slut under Skovdyrkerens besøg oplyser Thomas Dinesen, at man faktisk godt kan påtage sig at lave gulv af en skovejers eget træ. Det kræver kun, at han kan få skåret det i planker på et af de få tilbageværende danske savværker. Det var da et tilbud.
Se i øvrigt mere på//dinesen.com/da/ _blank> www.dinesen.com
By: Per Hilbert